House Addition Project 2006
-
- Co-Admin
- Posts: 1664
- Joined: Sat May 24, 2003 2:05 am
- Location: North Shore, Massachusetts USA
- Contact:
digging and digging
***
I met with the contractor and I dont want to remove all the work thats been done already...so I have compromised a bit here - although I think it will work out for both sides
the forms and footing will stay in place
as it stands the slab would normally be poured to just cover the footings but that would mean I have a 7'3" ceiling height in my basement/living space
to get closer to the magical 8' foot ceiling height in basement we will do the following
they will dig by hand several inches below the existing base of the footings
throw crushed stone in...a bit less than originally planned (but this is ?ok? as he said I have excellent subgrade material now)
then pour the 4" slab (concrete floor) in between the footings
this should net me an additonal 8"
so 8" + 7'3" should get me close to 7'11"
but then this is where I make out a bit
the kitchen I have is mostly being left as is structurally speaking - but has never made me quite happy as it slopes down over 1.5" over 12'
thats the kicker...after we realized they didnt dig deep enough I was assuming the ktichen would stay at that slope....it would normally cost too much to fix it (labor and onconvenience)
but the contractor has agreed...due to his mistake of not digging to the as planned depth...to jack up my kitchen to make it level whereby netting me another 1.5" of ceiling height in my new basement
so 7.3 + 8.0 + 1.5 maybe now gets me at least 8.0 ceiling height which is that magical number for me again
the only thing this compromise does to me is this....when I am standing on the slab in the future there will be a part of the footing left exposed about 8 inches in height and the depth to the poured walls....
not a big deal....maybe I can use that to my advantage somehow and place the hydraulic baseboard heating strips on top of it - I dunno
-john
I met with the contractor and I dont want to remove all the work thats been done already...so I have compromised a bit here - although I think it will work out for both sides
the forms and footing will stay in place
as it stands the slab would normally be poured to just cover the footings but that would mean I have a 7'3" ceiling height in my basement/living space
to get closer to the magical 8' foot ceiling height in basement we will do the following
they will dig by hand several inches below the existing base of the footings
throw crushed stone in...a bit less than originally planned (but this is ?ok? as he said I have excellent subgrade material now)
then pour the 4" slab (concrete floor) in between the footings
this should net me an additonal 8"
so 8" + 7'3" should get me close to 7'11"
but then this is where I make out a bit
the kitchen I have is mostly being left as is structurally speaking - but has never made me quite happy as it slopes down over 1.5" over 12'
thats the kicker...after we realized they didnt dig deep enough I was assuming the ktichen would stay at that slope....it would normally cost too much to fix it (labor and onconvenience)
but the contractor has agreed...due to his mistake of not digging to the as planned depth...to jack up my kitchen to make it level whereby netting me another 1.5" of ceiling height in my new basement
so 7.3 + 8.0 + 1.5 maybe now gets me at least 8.0 ceiling height which is that magical number for me again
the only thing this compromise does to me is this....when I am standing on the slab in the future there will be a part of the footing left exposed about 8 inches in height and the depth to the poured walls....
not a big deal....maybe I can use that to my advantage somehow and place the hydraulic baseboard heating strips on top of it - I dunno
-john
-
- Co-Admin
- Posts: 1664
- Joined: Sat May 24, 2003 2:05 am
- Location: North Shore, Massachusetts USA
- Contact:
theres gonna be lots of pics for this project
the new sliding glass door opening in the concrete walls is enough to fit a bike through ......hint hint hint
02/21/06
two cement trucks at once to pour the walls - wow!
02/23/06
forms removed
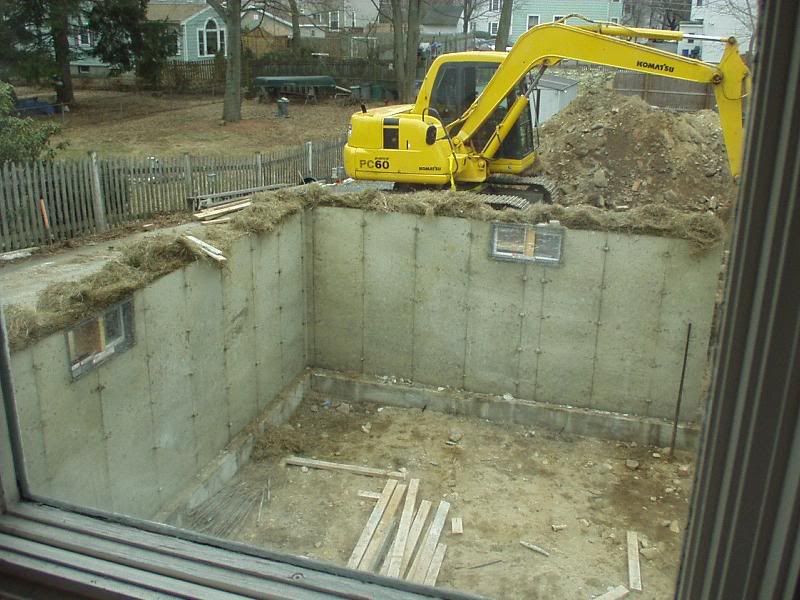
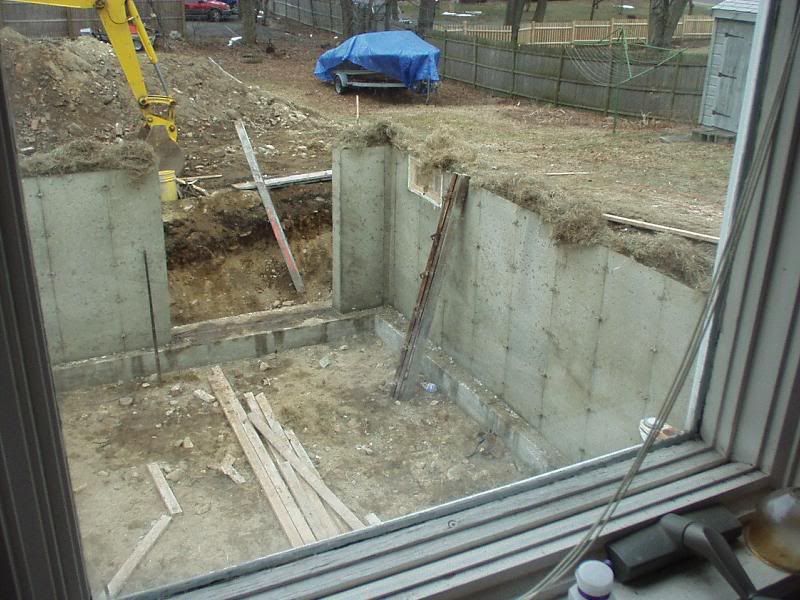
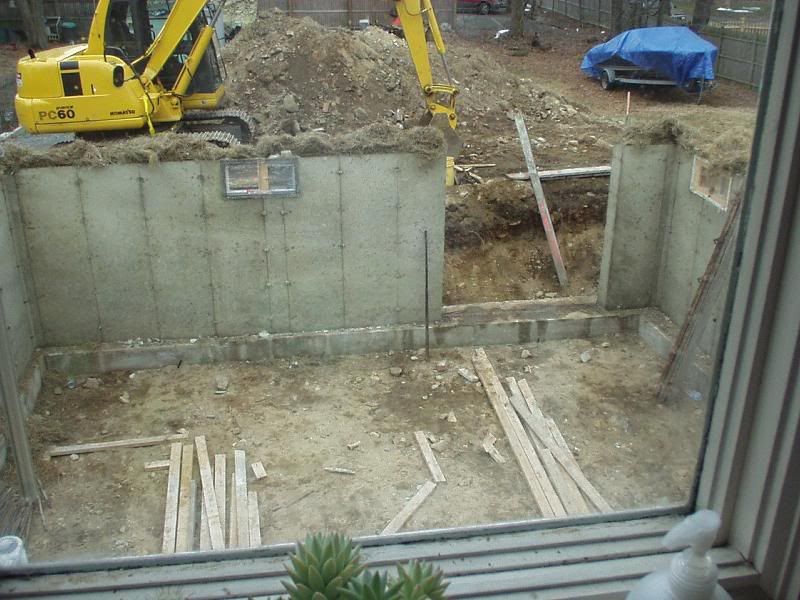
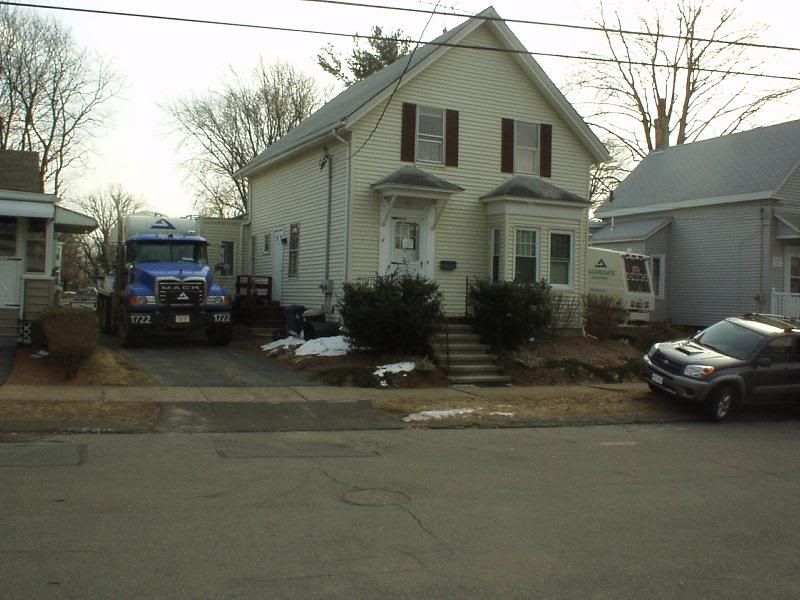
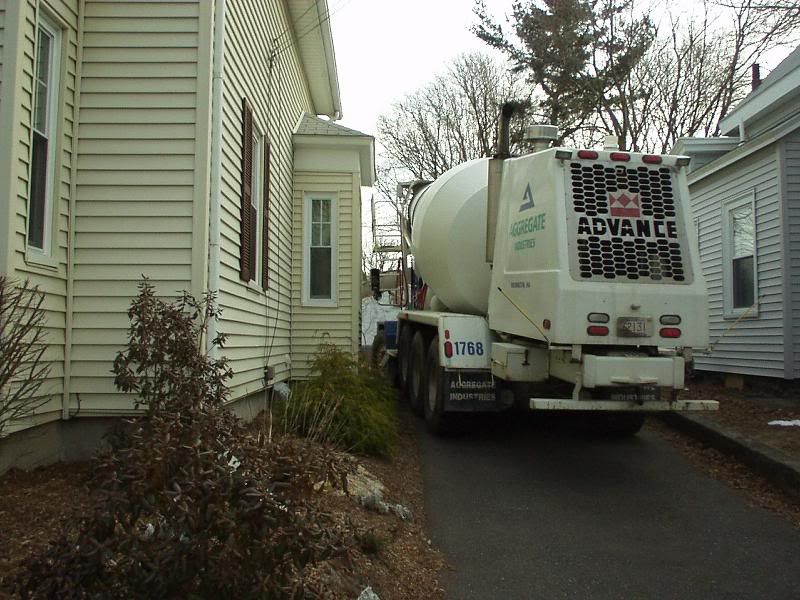
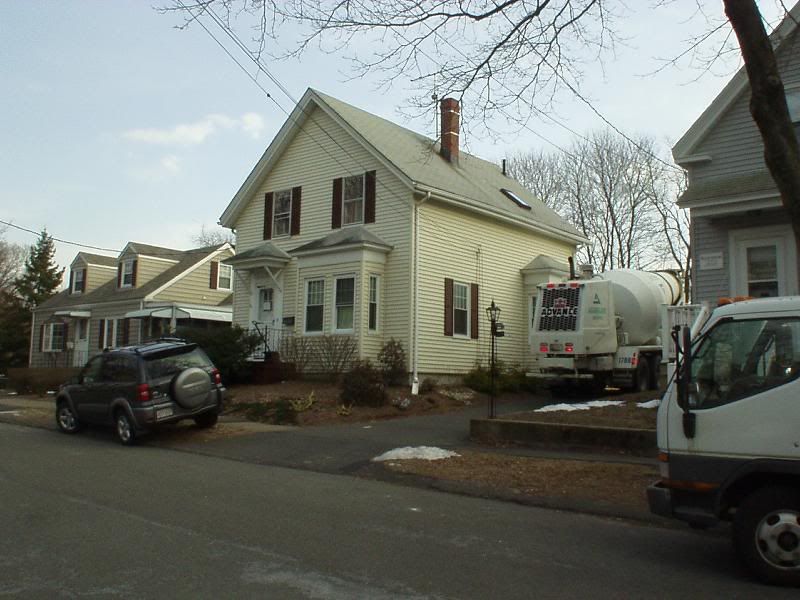
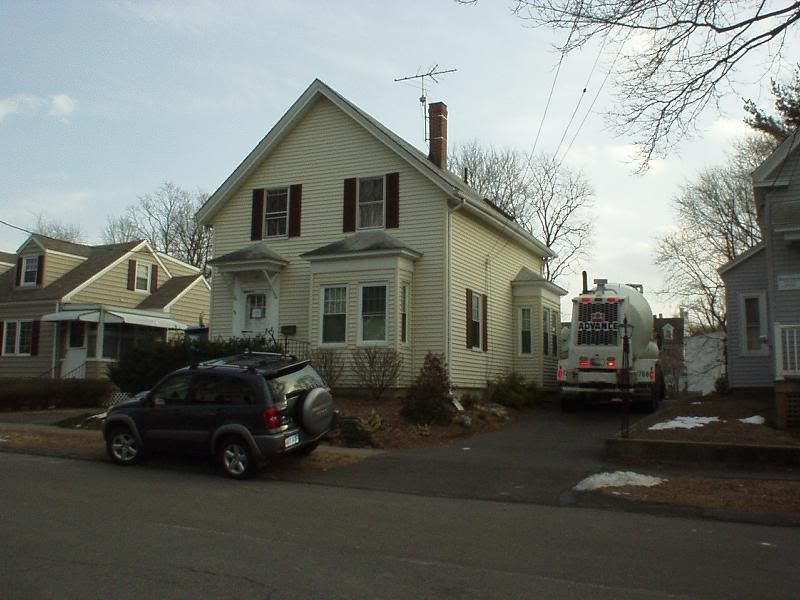
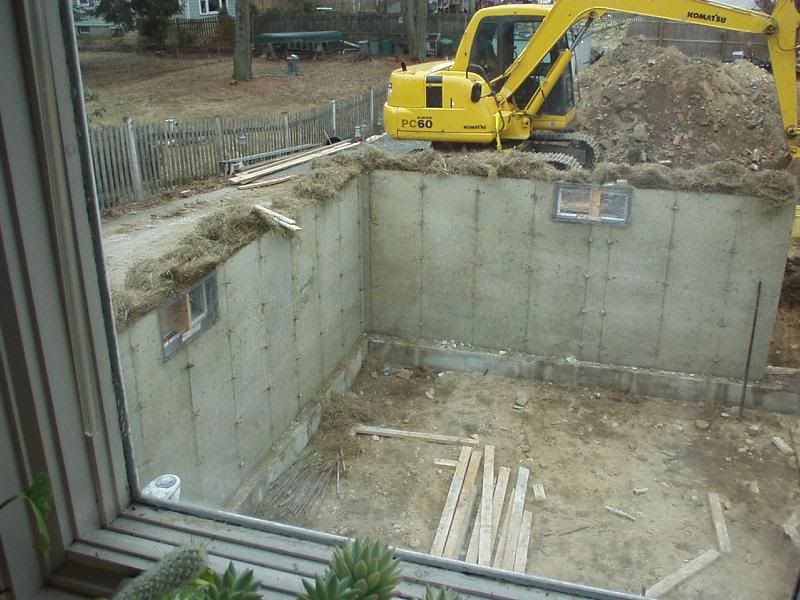
02/21/06
two cement trucks at once to pour the walls - wow!
02/23/06
forms removed
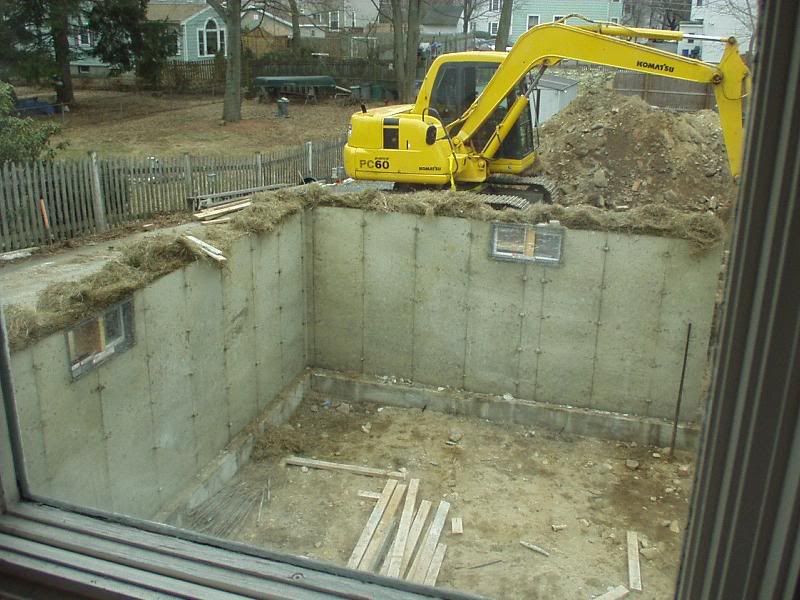
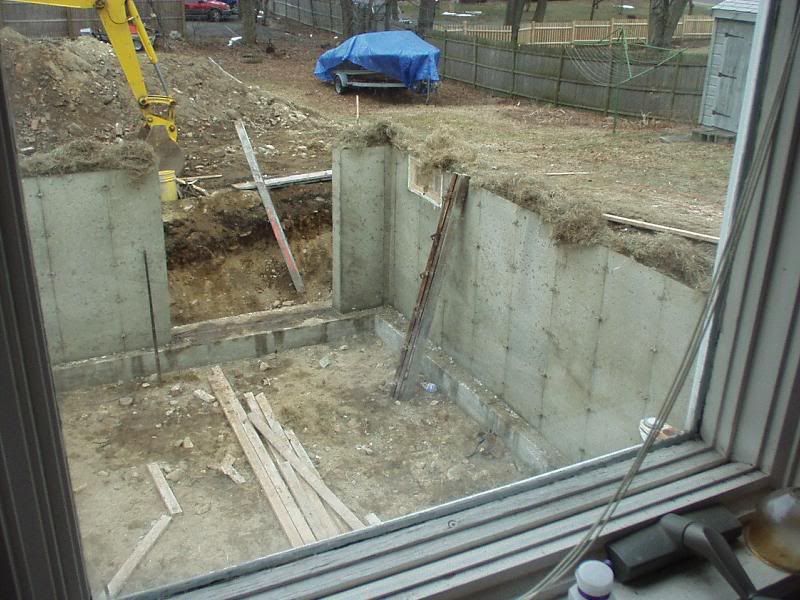
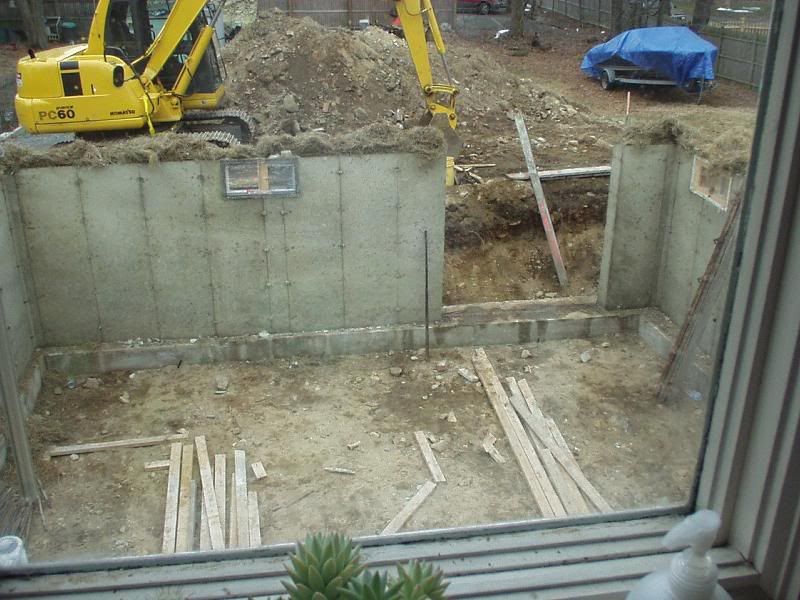
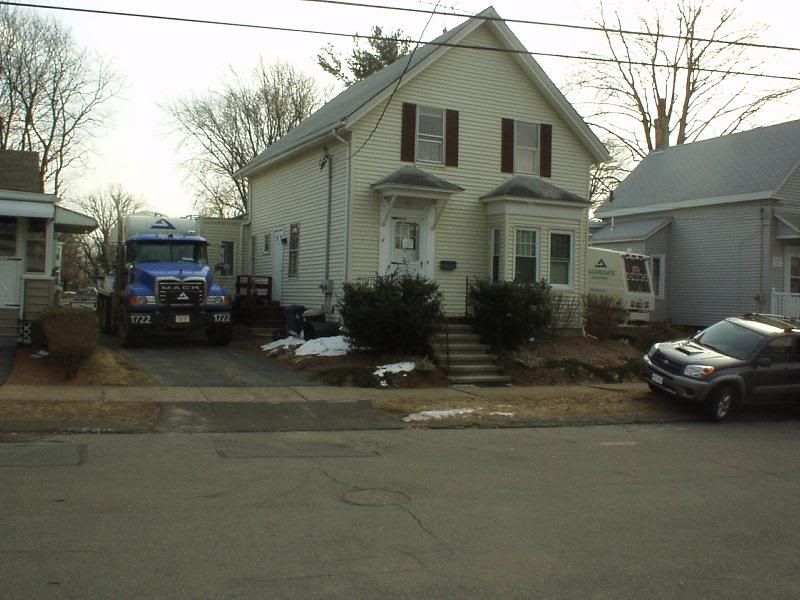
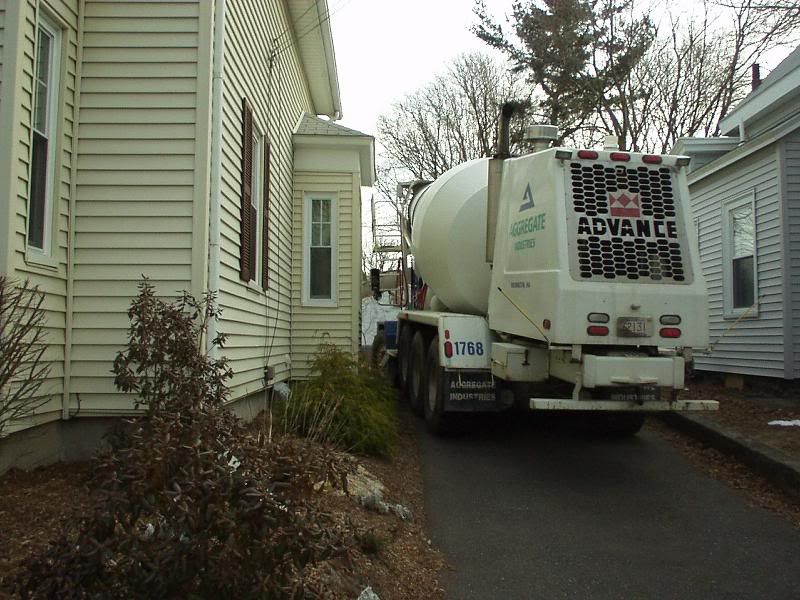
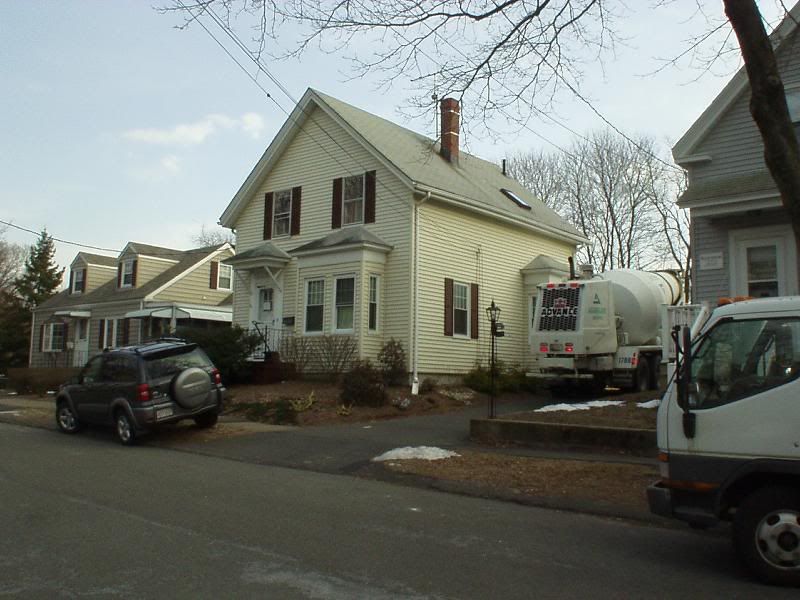
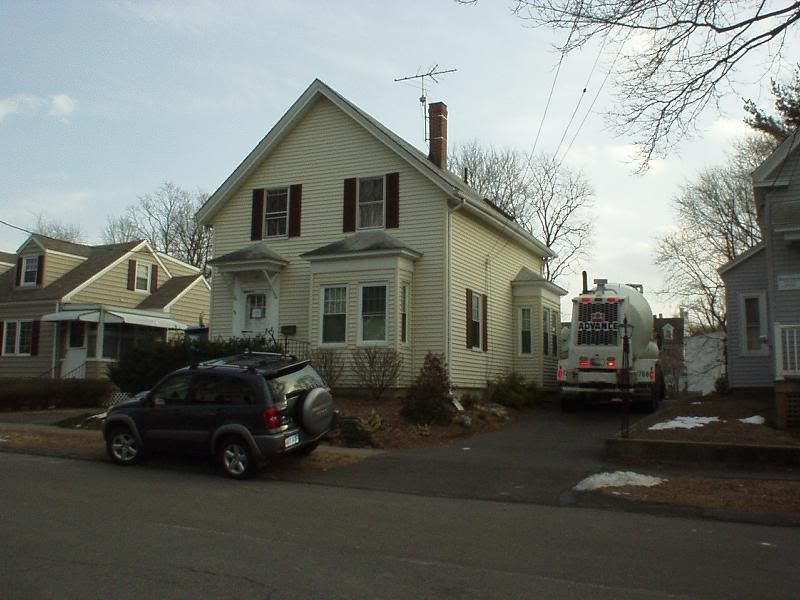
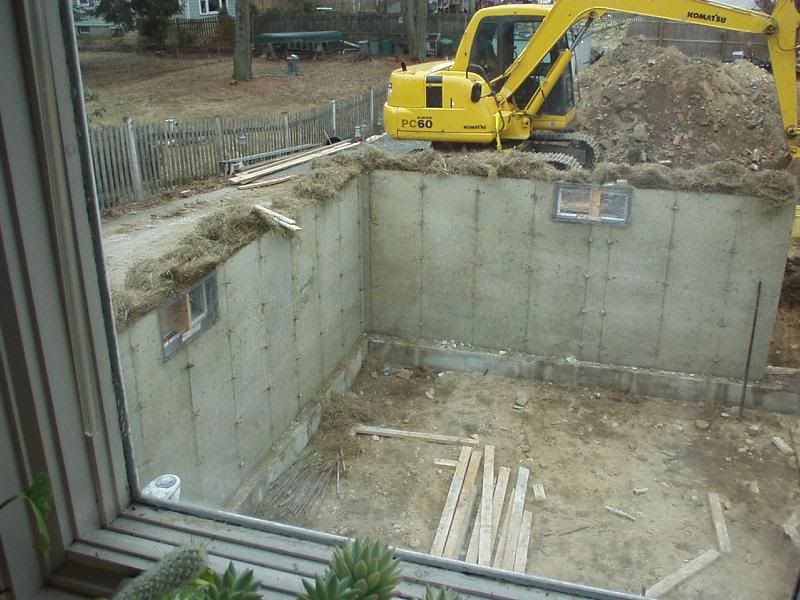
-
- New Poster
- Posts: 17
- Joined: Thu Jul 14, 2005 8:00 am
- Contact:
Looks like your extension is coming along now, that snow storm blew me away though. I am a structural draftsman and find it interesting to see the different building methods you guy use over in the states. The one thing that is the same is dodgy house builders, you get that everywhere. The amount of times that I get calls from residential builders that can’t read standard drawings is insane.
One thing I have never seen before is pouring the slab below the footings. Even if the sub grade is good you could have problems with the floor settling at a different rate to the walls over time. Talk to an engineer and get them to check it out. Might think about doweling some bars into the sides of the footings and getting thicker mesh to help prevent any serious cracking.
Still plenty of room for a garage too. :cool
One thing I have never seen before is pouring the slab below the footings. Even if the sub grade is good you could have problems with the floor settling at a different rate to the walls over time. Talk to an engineer and get them to check it out. Might think about doweling some bars into the sides of the footings and getting thicker mesh to help prevent any serious cracking.
Still plenty of room for a garage too. :cool
-
- 91 FZR250 3ln3 - 89 GS500e -

-
- Co-Admin
- Posts: 1664
- Joined: Sat May 24, 2003 2:05 am
- Location: North Shore, Massachusetts USA
- Contact:
thanks for the comments....this helps me in asking more questions with the contractor - I'll see about talking to a structural engineer or two to get some second thoughtsCiaran wrote:.....One thing I have never seen before is pouring the slab below the footings. Even if the sub grade is good you could have problems with the floor settling at a different rate to the walls over time. Talk to an engineer and get them to check it out. Might think about doweling some bars into the sides of the footings and getting thicker mesh to help prevent any serious cracking.
:cool
You mentioned the slab going below the footings...
I just want to clarify with you in case this makes a difference
the slab is to be 4 inches in total
with the footings a total of 10-12 inches already poured and set
this means the slab will be about 2 inches below and 2 inches along the sides of the footings
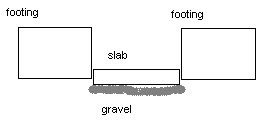
I say below the footings because usually the slab rests on top of the footings with the walls (strip footings, like yours) or the footing and the slab are done together in one pour (raft slab).
I don’t do cellars very often here but i had a look at some of our standard details and they showed a 200 thick slab (~8") with mesh top and bottom but it was also carrying 190mm reinforced blockwork.
I don’t doubt that your house will stand and not fall down or anything major like that. Its just the idea of the footing is to create a rigid platform for your slab, walls and roof so they all move relatively or together. Apart from solid rock, soil moves due to moisture content. It will also settle as the pressure from the building above compacts the ground. Without footings you can have one part of the house settling or rising while other areas remain static, cracking your walls, making doors and windows jam and the like. Or in your case the floor and walls settling at different rates due to varying pressures, maybe cracking your plaster board and architraves?
It may not be such of a problem if you have uncreative clays, ground is fairly solid or even if the slab is poured a couple of months after the footings. Its just allot easier to sort these things out now than it is further down the track. Remember the builder is always going to want to do things that are the cheapest and that required the least effort, not always a bad thing but not always the best.
My one bit of advice would be to contact that structural engineer and see what he says.
I don’t do cellars very often here but i had a look at some of our standard details and they showed a 200 thick slab (~8") with mesh top and bottom but it was also carrying 190mm reinforced blockwork.
I don’t doubt that your house will stand and not fall down or anything major like that. Its just the idea of the footing is to create a rigid platform for your slab, walls and roof so they all move relatively or together. Apart from solid rock, soil moves due to moisture content. It will also settle as the pressure from the building above compacts the ground. Without footings you can have one part of the house settling or rising while other areas remain static, cracking your walls, making doors and windows jam and the like. Or in your case the floor and walls settling at different rates due to varying pressures, maybe cracking your plaster board and architraves?
It may not be such of a problem if you have uncreative clays, ground is fairly solid or even if the slab is poured a couple of months after the footings. Its just allot easier to sort these things out now than it is further down the track. Remember the builder is always going to want to do things that are the cheapest and that required the least effort, not always a bad thing but not always the best.
My one bit of advice would be to contact that structural engineer and see what he says.
-
- 91 FZR250 3ln3 - 89 GS500e -

-
- Co-Admin
- Posts: 1664
- Joined: Sat May 24, 2003 2:05 am
- Location: North Shore, Massachusetts USA
- Contact:
yummm yumm yumm yummm crunch crunch
after raising my kitchen up to be level...we found insect damage - likely carpenter ants
frickn little bastards
I think the damage is from quite some time ago and there is no new activity or any evidence to support such...but I'll be hiring an exterminator just in case
frickn little bastards
I think the damage is from quite some time ago and there is no new activity or any evidence to support such...but I'll be hiring an exterminator just in case
-
- Co-Admin
- Posts: 1664
- Joined: Sat May 24, 2003 2:05 am
- Location: North Shore, Massachusetts USA
- Contact:
Its been a while since I last posted - mostly because I have been raising the kitchen myself - in effort to save money.
I also changed the interior plans somewhat - and that changed the type of I-Beam and the floor joists - which changees height as well of the overall structure / ceilings etc.
Used mostly pressure treated wood as it is under the kitchen where there is still the possibility of ground moisture.
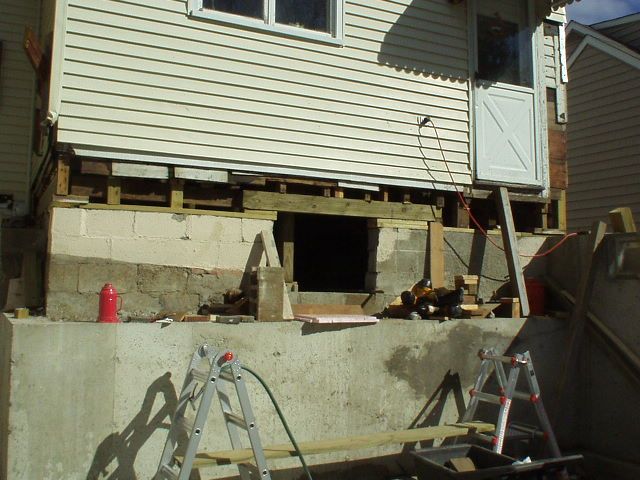
the old beam under the kitchen and new beam in background - previously there was just some field stone under one end of the old beam - I dug out 3 feet and laid concrete and cinderblock w/steel post for added strength and support
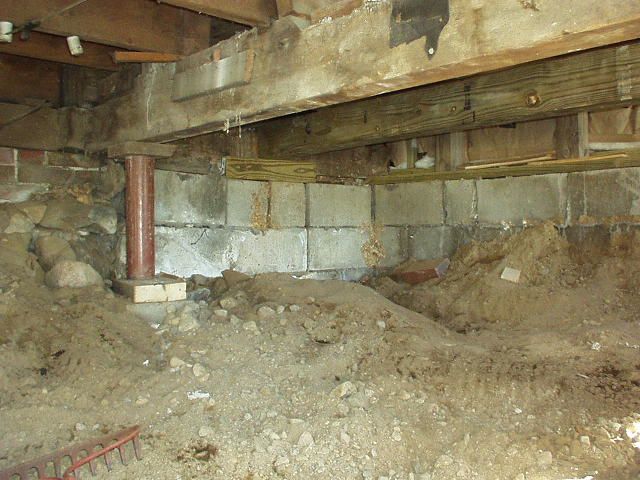
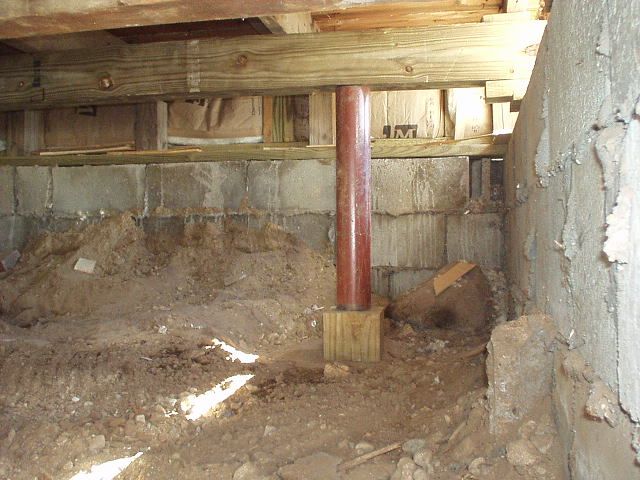
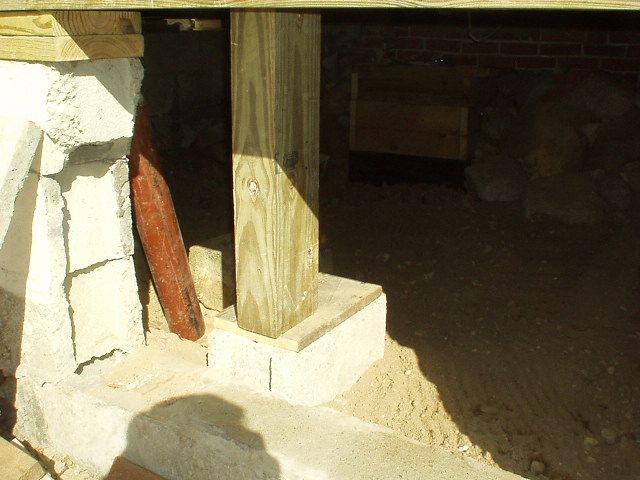
the old coal entrance under the kitchen - the 2x8's enclose the interior accessible shelves in my office
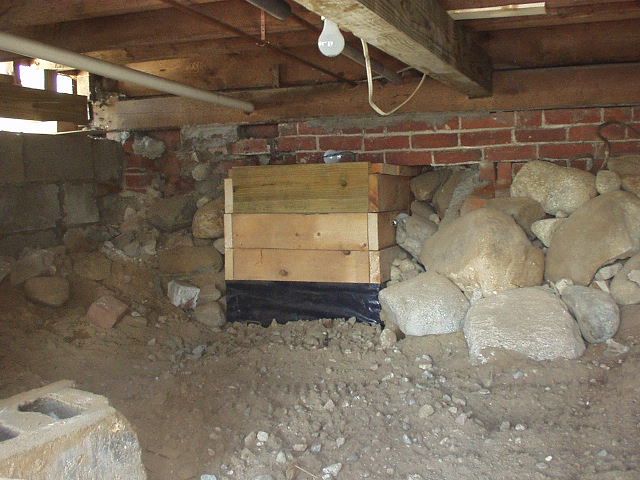
the left edge of the kitchen after ripping out the old sill - the old sill was insect damage and rot
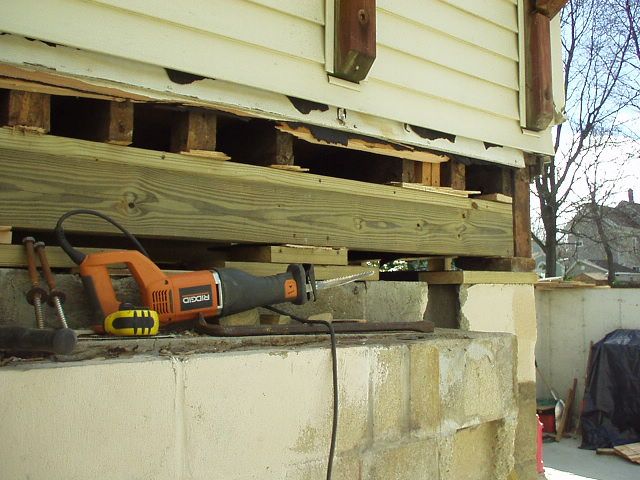
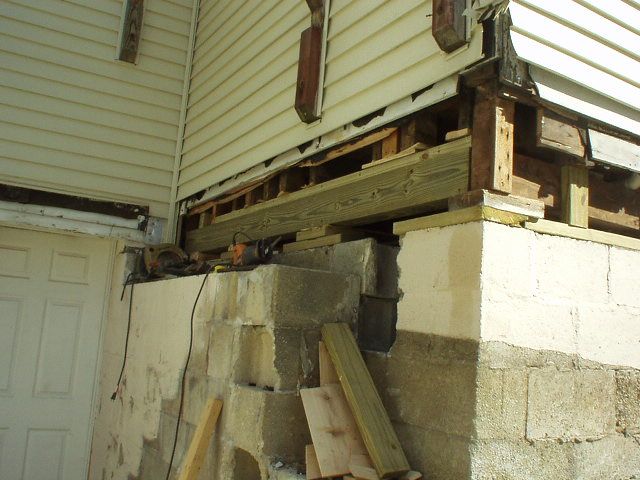
The inside of my office - where I poke a hole into the wall where the old coal loading window was (in the cellar) - I'll use this space for the dvd player and tivo etc - this whole thing was overbuilt with 2x8's and almost 4 bags of concrete on the outside perimeter and base
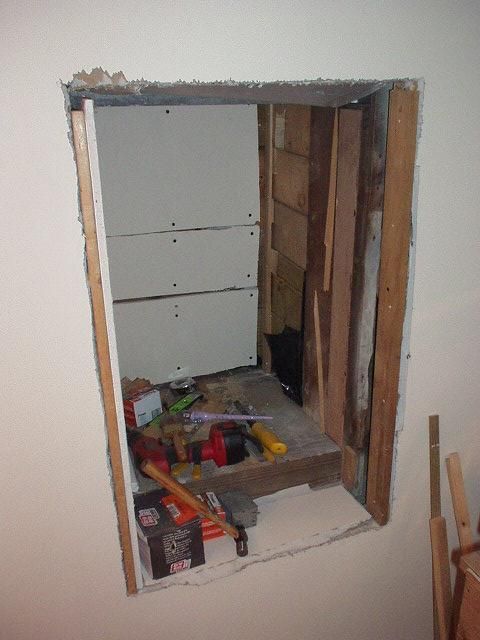
My new wonder ladder - including dvd on how to use the thing
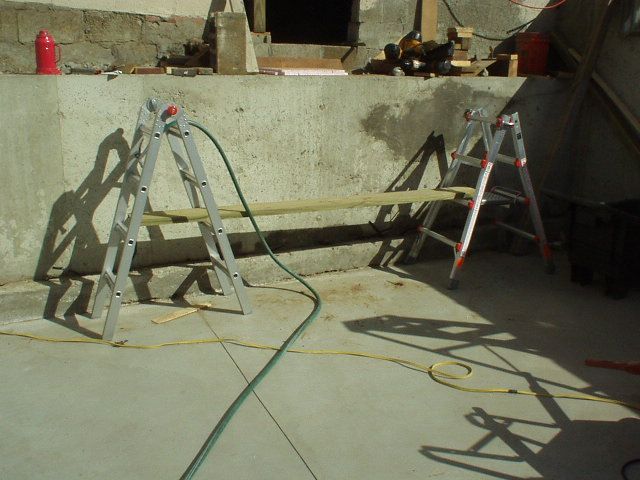
The steel I-Beam #87 - all 26 feet of it and 2600lbs.
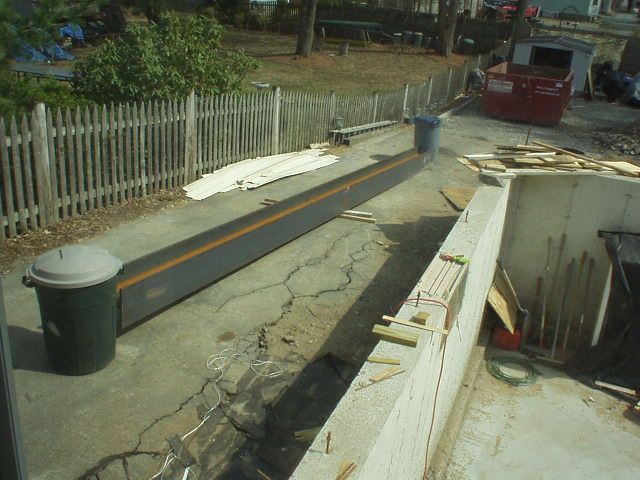
Was lifted into place quite easily with the hitachi. Ya know every house should have an I-Beam like this. It will be lagged and welded into place in the next day or so. Thats Corey helping guide while i do the important recording of the event. Corey is MUCH stronger than he looks.
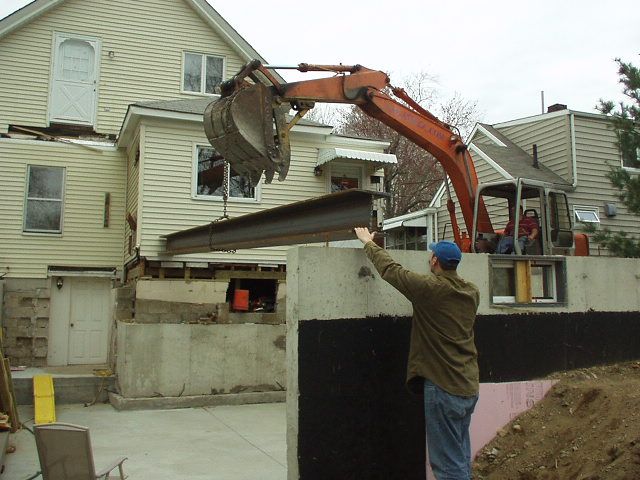
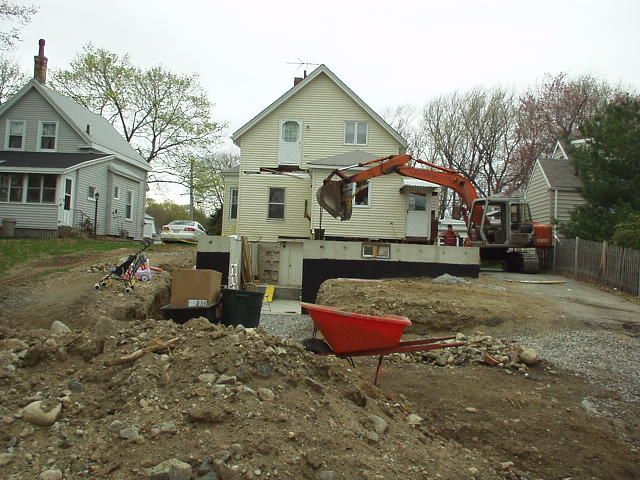
I also changed the interior plans somewhat - and that changed the type of I-Beam and the floor joists - which changees height as well of the overall structure / ceilings etc.
Used mostly pressure treated wood as it is under the kitchen where there is still the possibility of ground moisture.
the old beam under the kitchen and new beam in background - previously there was just some field stone under one end of the old beam - I dug out 3 feet and laid concrete and cinderblock w/steel post for added strength and support
the old coal entrance under the kitchen - the 2x8's enclose the interior accessible shelves in my office
the left edge of the kitchen after ripping out the old sill - the old sill was insect damage and rot
The inside of my office - where I poke a hole into the wall where the old coal loading window was (in the cellar) - I'll use this space for the dvd player and tivo etc - this whole thing was overbuilt with 2x8's and almost 4 bags of concrete on the outside perimeter and base
My new wonder ladder - including dvd on how to use the thing
The steel I-Beam #87 - all 26 feet of it and 2600lbs.
Was lifted into place quite easily with the hitachi. Ya know every house should have an I-Beam like this. It will be lagged and welded into place in the next day or so. Thats Corey helping guide while i do the important recording of the event. Corey is MUCH stronger than he looks.

- FZRDude
- Co-Admin
- Posts: 4807
- Joined: Tue Jan 13, 2004 3:20 am
- Location: North-Left Coast, USA
- Contact:
That is an awefully small office for such a big guy...John wrote:The inside of my office - where I poke a hole into the wall where the old coal loading window was (in the cellar)...... this whole thing was overbuilt with 2x8's and almost 4 bags of concrete on the outside perimeter and base

There are some who call me........Tim?
In Memory Of John "Silver" Douglas (Dec. 08, 2008) R.I.P. My Friend.

In Memory Of John "Silver" Douglas (Dec. 08, 2008) R.I.P. My Friend.




-
- New Poster
- Posts: 17
- Joined: Thu Jul 14, 2005 8:00 am
- Contact:
-
- Co-Admin
- Posts: 1664
- Joined: Sat May 24, 2003 2:05 am
- Location: North Shore, Massachusetts USA
- Contact:
check out
http://www.coolhouseplans.com
then on the right hand side look under the 2nd bold heading for
Garage Plans Only
This is a great site to look over possibilities for garages not to mention house styles.
The best part is it is cheap for the plans rather than hiring a architect for a canned solution.
http://www.coolhouseplans.com
then on the right hand side look under the 2nd bold heading for
Garage Plans Only
This is a great site to look over possibilities for garages not to mention house styles.
The best part is it is cheap for the plans rather than hiring a architect for a canned solution.
-
- Co-Admin
- Posts: 1664
- Joined: Sat May 24, 2003 2:05 am
- Location: North Shore, Massachusetts USA
- Contact:
....the framing crew owner is spanish with portuguese crew. Very hard working guys.
Oh heres the best part...Corey walked over...and was listenting to what they were talking about. He's like....hey....that not spanish thats portuguese. lol....Corey knows portuguese from his portuguese girlfriend.
So I had him translating for me for a while.
Oh heres the best part...Corey walked over...and was listenting to what they were talking about. He's like....hey....that not spanish thats portuguese. lol....Corey knows portuguese from his portuguese girlfriend.
So I had him translating for me for a while.
- FZRDude
- Co-Admin
- Posts: 4807
- Joined: Tue Jan 13, 2004 3:20 am
- Location: North-Left Coast, USA
- Contact:
Okay, I have a question. On the upstairs.... How the heck are the stairs gonna work with that door to the outside? Are the stairs headed towards the door or away?
OR
Are you just going to relocate the door somewhere else?
OR
Are you just going to relocate the door somewhere else?
There are some who call me........Tim?
In Memory Of John "Silver" Douglas (Dec. 08, 2008) R.I.P. My Friend.

In Memory Of John "Silver" Douglas (Dec. 08, 2008) R.I.P. My Friend.




-
- Co-Admin
- Posts: 1664
- Joined: Sat May 24, 2003 2:05 am
- Location: North Shore, Massachusetts USA
- Contact:
As seen in the pics...the upstairs door will exit to the immediate left in a hallway that leads to a outside door...which then will lead to a set of EXTERIOR stairs to get to ground level.
To the immediate right of the upstairs door - there will be a set of stair that lead upward to the 27'x35' loft.
To the immediate right of the upstairs door - there will be a set of stair that lead upward to the 27'x35' loft.